Sheet metal manufacturing is a vital process for creating the metal parts we use every day, from kitchen appliances to car frames. Sometimes, though, it can feel overwhelming to figure out how to boost efficiency and precision in such a demanding industry. If you’ve ever wondered about making things smoother, faster, and more accurate, you’re not alone!
In this article, we’ll explore everything from what CNC technology is to why it’s a big deal in sheet metal manufacturing and how you can use it to achieve better quality and faster turnaround times. Stick around to learn how each aspect of CNC tech can help you optimize your production process!
Understanding CNC Technology In Sheet Metal Manufacturing
Sheet metal manufacturing benefits greatly from CNC precision. This technology uses computerized controls to guide cutting, forming, and shaping operations with incredible accuracy. It ensures uniform parts, reduces production times, and lowers waste. By relying on CNC-driven methods, companies gain a competitive edge in quality, cost, and delivery speed.
CNC Fundamentals
CNC, or Computer Numerical Control, refers to machines directed by computerized instructions. These instructions handle tasks such as cutting and shaping metal. In sheet metal manufacturing, CNC offers precision, scalability, and consistency. This technology transforms design files into real-world, accurately produced metal parts.
CNC Machine Components
A CNC system includes a controller, motors, cutting tools, and software. In sheet metal manufacturing, each component works in harmony. The software interprets the design, the motors drive the cutting tools, and the controller ensures every movement aligns perfectly with the programmed coordinates.
CNC In Industrial Settings
CNC machines are used in various settings, from automotive factories to aerospace plants. In sheet metal manufacturing, these machines handle tasks like punching, bending, and laser cutting. The result is improved throughput, minimized waste, and a more reliable, cost-effective production process.
Enhancing Precision And Accuracy
CNC technology offers remarkable accuracy in sheet metal manufacturing. This precision means the metal parts fit together exactly as they should, making everything safer and more reliable. Tiny mistakes in manual processes can turn into big problems, but CNC reduces those errors dramatically.
- Each cut aligns with digital blueprints.
- Parts remain consistent even in large batches.
- Complex shapes are achievable without guesswork.
With CNC, you get almost perfect repeatability because the entire process is guided by digital instructions. Once you dial in your specifications, every piece produced follows the same pattern, boosting overall product quality.
Faster Production Times
In many industries, time truly is money. By automating various steps, CNC machines can speed up sheet metal manufacturing cycles. They handle multiple operations—like cutting, drilling, and forming—without the need to move parts between different machines. This consolidation of tasks saves hours if not days.
- Multiple machining steps happen in one setup.
- Robots and CNC work together to automate loading/unloading.
- Real-time monitoring to spot issues before they cause delays.
Because CNC machines don’t need breaks or shift changes, they can run around the clock. This 24/7 productivity can drastically improve your turnaround times and help you meet tight deadlines with ease.
Versatility In Complex Designs
When you’re dealing with complicated structures—like intricate brackets or specialized enclosures—CNC technology shines. Traditional manufacturing methods might struggle with tight corners or oddly shaped cutouts, but CNC can handle them with simplicity. As the design becomes more complex, the computer can still guide the tool path precisely.
This benefit is crucial in sheet metal manufacturing, where one-of-a-kind prototypes or custom parts are increasingly in demand. From unique art installations to specialized medical equipment, CNC provides a level of flexibility that manual processes can’t match.
Reduced Material Waste
Traditional manufacturing often involves a lot of trial and error. With CNC, your design is tested virtually before a single cut is made. That means less scrap metal and fewer wasted materials. Efficient sheet metal manufacturing not only saves money but also helps the environment by reducing the overall carbon footprint.
CNC machines work with high accuracy, so they only cut what’s needed. The rest of the metal remains intact. Over time, this can lead to significant cost savings, especially if you produce large volumes. Because you’re not tossing out as much leftover metal, your bottom line benefits, and your sustainability efforts improve too.
Consistent Quality Control
Quality control is vital in any manufacturing process, especially in sheet metal manufacturing.Customers expect parts that meet exact standards, whether it’s thickness, cut dimensions, or overall integrity. CNC technology allows you to set those standards and repeat them precisely for each batch.
To illustrate how consistency can improve overall output, here’s a quick table:
Factor | Manual Process Average | CNC Process Average |
---|---|---|
Error Rate (%) | 5 | 0.5 |
Daily Output (units) | 100 | 300 |
Scrap Rate (%) | 10 | 2 |
Setup Time (hours) | 4 | 1 |
By automating measurement and adjustments, CNC machines ensure each piece matches the design. You spend less time double-checking or fixing errors and more time focusing on productivity and customer satisfaction.
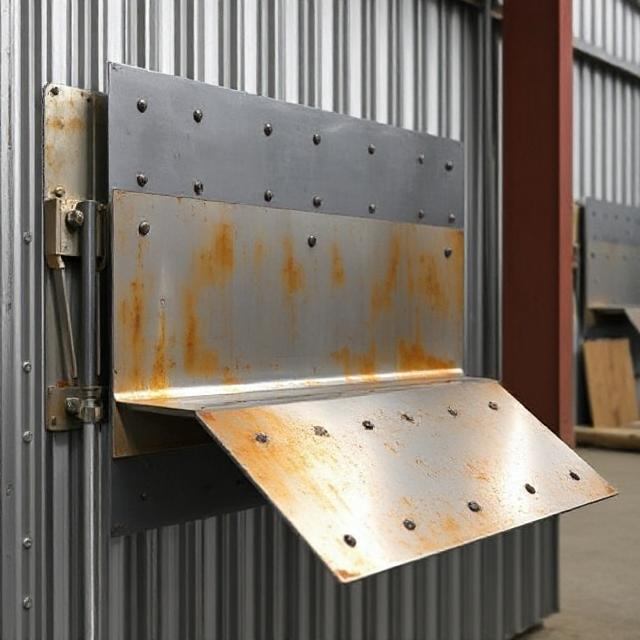
User-Friendly Interfaces
Modern CNC machines are surprisingly easy to operate, especially for sheet metal manufacturing. The controls often come with intuitive software that helps operators set parameters quickly. Even someone new to CNC can learn basic functions after some training. This user-friendly approach shortens the learning curve and reduces operator mistakes.
- Graphical software guides you through setup steps.
- Alerts and prompts minimize the risk of errors.
- Touchscreen displays simplify navigation and programming.
With a more approachable interface, shops can cross-train employees. This flexibility prevents bottlenecks if a key operator is absent and can improve overall efficiency.
Cost-Effectiveness Over The Long Term
While CNC machines can be a big investment, the return often justifies the price. When you factor in reduced labor costs, fewer errors, and less waste, the long-term savings are considerable. Sheet metal manufacturing involves recurring batches and repetitive tasks, which are exactly the kinds of jobs CNC excels at.
You also have the added bonus of faster product turnaround. This can lead to higher customer satisfaction, repeat business, and a stronger reputation. Over time, the combination of increased productivity and consistent quality can significantly boost your bottom line.
Scalability For Varying Production Volumes
One of the main perks of CNC in sheet metal manufacturing is its ability to scale. Whether you need 10 parts for a prototype run or 10,000 parts for a large product launch, CNC can handle it. You don’t have to change tooling or machines dramatically to switch from a small batch to a large one.
Additionally, CNC machines make it easy to revise designs. If a client requests a minor tweak, you can often update the digital file and continue production right away. This flexibility offers a competitive advantage for companies that handle diverse or rapidly evolving product lines.
Safer Working Environments
Manufacturing can sometimes be risky, especially when it involves heavy machinery or sharp tools. CNC technology helps reduce those risks because it automates many tasks. Operators spend less time near moving parts and cutting tools, which means fewer chances for accidents.
- Automated doors and guards protect operators.
- Sensors stop machines if irregularities occur.
- Less manual handling of large or hot metal sheets.
By focusing on worker safety, companies also boost morale. Employees feel more comfortable and confident, contributing to better overall performance and lower turnover rates.
Adapting To Future Technologies
CNC machines aren’t just about mechanical processes anymore. They increasingly integrate with the Internet of Things (IoT) and AI systems. In sheet metal manufacturing, this means real-time data tracking, predictive maintenance, and advanced analytics on machine usage. With these add-ons, you can forecast production needs and spot issues before they become major problems.
Staying current with CNC technology also means you can incorporate new cutting methods or automation upgrades as they emerge. This forward-thinking approach keeps your operations efficient and positions you to adapt quickly in a fast-changing market.
Training And Workforce Development
One concern about advanced technology is the fear that it will replace human workers. In reality, CNC technology in sheet metal manufacturing shifts the skill set required. Instead of manual labor, more attention goes to programming, monitoring, and maintenance. Companies can invest in training to help operators upgrade their skills and grow their careers.
- Training sessions for CAD/CAM software
- Workshops focusing on machine calibration
- Ongoing courses in safety and best practices
Providing these development paths not only keeps your workforce engaged but also prepares your company to handle future technological changes smoothly.
Real-World Industries Benefiting From CNC
The advantages of CNC in sheet metal manufacturing aren’t limited to one sector. Automotive, aerospace, medical, and consumer electronics all rely on CNC for speed and consistency. For instance, aircraft parts demand extreme precision for safety reasons. Automotive makers need to roll out cars on tight schedules. Electronics manufacturers require intricate metal housings and brackets.
Each of these industries benefits from the same core features: enhanced accuracy, reduced waste, and quick turnaround times. As more industries discover the perks, the demand for CNC in sheet metal manufacturing is only growing.
Factors To Consider When Implementing CNC
Before jumping into CNC, there are a few things to think about. First, you need a proper budget. CNC machines, software, and maintenance can be pricey. Second, you’ll want to plan for employee training to get the most out of your investment. Third, consider future expansion needs. If you expect rapid growth, choose CNC systems that can scale with you.
You’ll also want to partner with reliable suppliers. A quality CNC machine can last for years, but only if you have proper support and spare parts. Researching trusted brands and reading reviews can help you avoid costly mistakes. For more details, you can check reputable resources like XC Machining or Modern Machine Shop.
Conclusion
CNC technology has become a transformative force in sheet metal manufacturing, driving greater accuracy, speed, and cost savings. By automating tasks that used to be manual, CNC frees up human operators for more strategic roles, all while boosting output. From tighter tolerances to safer work conditions, CNC offers a comprehensive solution for modern industry demands.
Ultimately, when it comes to sheet metal manufacturing, CNC is a game-changer. It reduces waste, speeds up production, and ensures repeatable results. Whether you’re a small shop or a large enterprise, implementing CNC can provide tangible benefits that set you apart in a competitive market.
FAQ
How long does it take to learn CNC operation?
Most operators can grasp basic functions in a few weeks of hands-on training, though mastering more advanced programming could take several months.
Is CNC only for large-scale manufacturers?
No. Even small workshops benefit from the precision and repeatability of CNC technology, especially if they frequently handle custom orders or complex parts in sheet metal manufacturing.
Does CNC completely remove the need for manual labor?
Not entirely. You still need skilled workers for programming, maintenance, and quality checks. CNC just shifts the focus from manual tasks to more analytical and technical roles.